Understanding Reciprocating Pumps: A Comprehensive Overview for Businesses
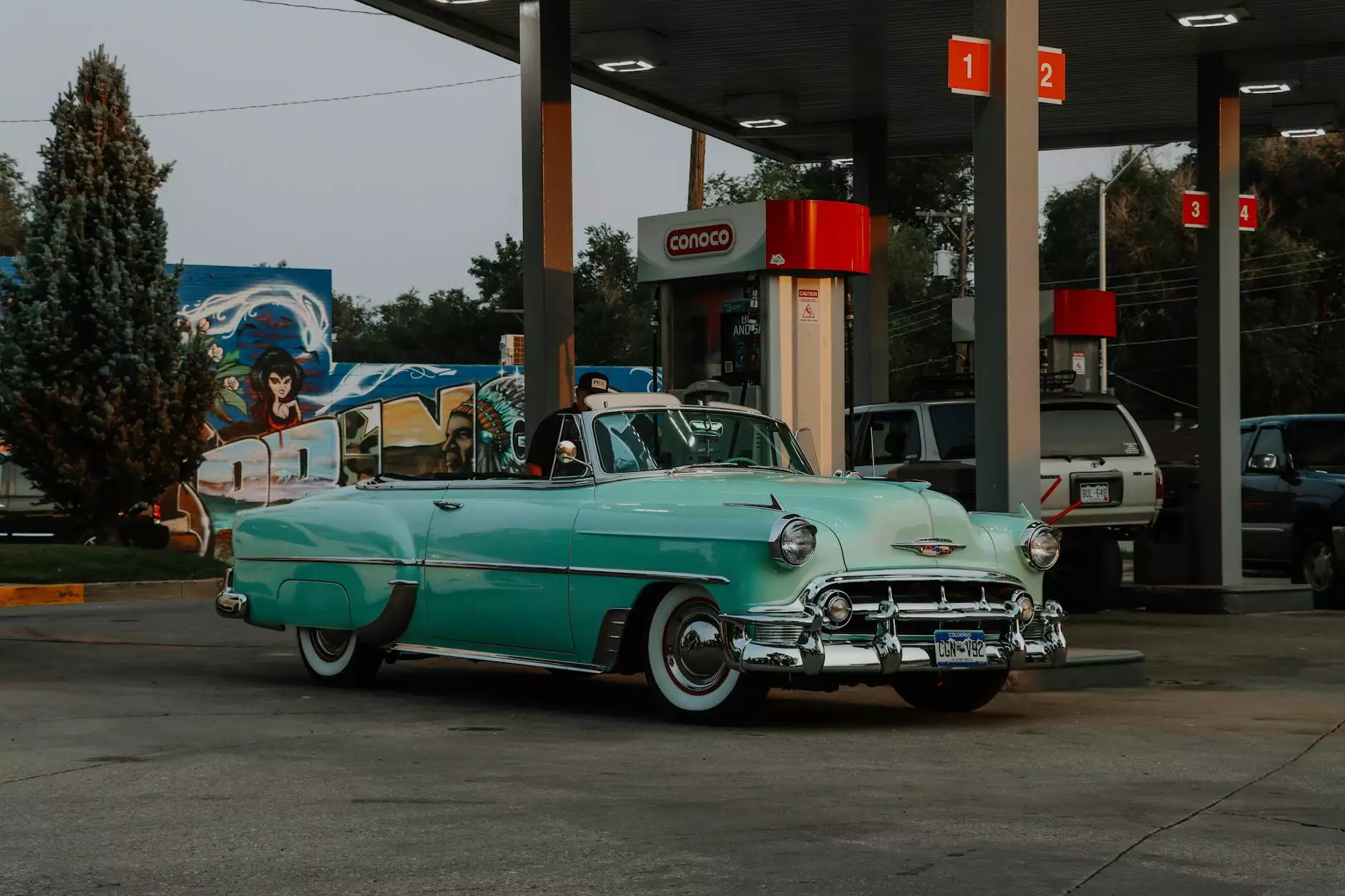
In the modern industrial landscape, the efficiency and reliability of machinery play a crucial role in various sectors. Among these, the reciprocating pump has emerged as a dependable solution for the transportation of fluids in diverse applications. This article delves deep into the intricacies of reciprocating pumps, their applications in different fields, and their significance in enhancing productivity and reducing downtime.
What is a Reciprocating Pump?
A reciprocating pump is a type of positive displacement pump that uses a back-and-forth (reciprocating) motion to move fluids. This mechanism operates by drawing fluid into a cylinder during one phase of the stroke, and then expelling it during the subsequent stroke, creating a consistent and controlled flow of liquid. Reciprocating pumps are known for their ability to handle high pressures and their effectiveness in transferring both thin and thick fluids.
Key Components of Reciprocating Pumps
To understand how reciprocating pumps work, it's essential to familiarize ourselves with their key components:
- Piston or Plunger: The primary moving part that creates the suction and discharge action.
- Cylinder: The chamber where the fluid is drawn and expelled.
- Inlet and Outlet Valves: These check valves prevent backflow while allowing fluid to enter and exit the cylinder.
- Power Source: Typically an electric motor or internal combustion engine that drives the piston movement.
- Frame or Base: Provides structural integrity to the pump assembly.
Types of Reciprocating Pumps
Reciprocating pumps can be categorized based on their design and the type of motion they utilize:
1. Piston Pumps
Piston pumps are characterized by a piston that moves within a cylinder. They are widely used in applications requiring high pressure.
2. Plunger Pumps
Plunger pumps employ a plunger instead of a piston and are highly efficient in handling corrosive fluids or high-viscosity materials.
3. Diaphragm Pumps
These pumps use a diaphragm that flexes to create a pumping action, making them ideal for applications requiring leak-free operations and handling toxic fluids.
Applications of Reciprocating Pumps
Reciprocating pumps find their application across various industries, showcasing their versatility and reliability. Here are some notable sectors that benefit from this technology:
Auto Repair
In auto repair shops, reciprocating pumps are essential for fueling, fluid transfer, and even brake system diagnostics. They ensure precise fluid delivery and enhanced operational efficiency.
Farm Equipment Repair
Farm machinery often requires robust pumping solutions for transferring fertilizers, irrigation water, and fuel. Reciprocating pumps help farmers manage these resources effectively, contributing to improved yield and sustainable practices.
Structural Engineering
In construction and structural engineering, reciprocating pumps play a critical role in concrete mixing, grout pumping, and soil stabilization. They help in maintaining consistent material flow, crucial for structural integrity and safety.
Advantages of Using Reciprocating Pumps
The adoption of reciprocating pumps offers numerous advantages, which include:
- High Efficiency: Capable of delivering liquids at high pressure with minimal energy loss.
- Versatility: Can handle a wide variety of fluids including viscous, corrosive, and abrasive substances.
- Reliable Flow Control: Provides steady and controllable fluid flow, ideal for precision applications.
- Durability: Built to withstand harsh operating conditions, making them suitable for long-term use.
Maintenance Tips for Reciprocating Pumps
To ensure longevity and optimal performance from reciprocating pumps, proper maintenance is essential. Here are some key practices:
1. Regular Inspection
Conduct periodic inspections to check for wear and tear, leakage, and other operational issues. Early detection can prevent major breakdowns.
2. Lubrication
Ensure that all moving parts are properly lubricated to minimize friction and wear. Follow the manufacturer's recommendations regarding lubrication intervals.
3. Seal Replacement
Regularly check and replace seals to prevent leakage, which can not only waste fluids but also cause damage to the pump components.
4. Check Valves
Inspect inlet and outlet valves for proper functioning. Replace any faulty valves to maintain the pump's efficiency and prevent backflow.
The Future of Reciprocating Pumps
The landscape of machinery is continuously evolving, and reciprocating pumps are no exception. With advances in technology, the future of reciprocating pumps looks promising:
- Smart Technology Integration: Incorporating IoT for real-time monitoring and predictive maintenance.
- Energy Efficiency: Development of more efficient motors and designs that consume less power.
- Eco-friendly Materials: Transitioning towards environmentally friendly materials to reduce the ecological footprint.
Conclusion
The reciprocating pump stands out as a vital piece of equipment in many industries, thanks to its robust performance and adaptability. As industries face increasing demands for efficiency and reliability, understanding and leveraging the benefits of reciprocating pumps will be crucial. At Michael Smith Engineers, we pride ourselves on providing superior engineering solutions tailored to your needs. Whether you are involved in auto repair, farm equipment repair, or structural engineering, our expertise in reciprocating pumps can help enhance your operational efficiency.
By investing in proper maintenance and utilizing the right technology, businesses can ensure that their reciprocating pumps remain a cornerstone of their productivity and dependability. If you’re looking to enhance your operation with reliable pumping solutions, don’t hesitate to reach out to us.